Steve Bowman
Well-Known Member
Then I braced the bushings and tweaked them a little to get the shaft to slide freely between them, and started welding.
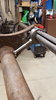
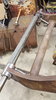
I was not having a lot of luck keeping my torch angle right while welding around the bushings, so they lack some cosmetically, but I think they are sound.


I kept moving the shaft while welding and sort of moving from place to place on the bushings. I did preheat here also like I did on the boom. In the end, I could still slide the shaft between the bushings.
Certainly unconventional, but I think it worked ok. Best of all - on budget!. lol
The fab shop hasn't gotten to my plates yet, so nothing new on the quick attach plate.
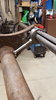
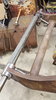
I was not having a lot of luck keeping my torch angle right while welding around the bushings, so they lack some cosmetically, but I think they are sound.


I kept moving the shaft while welding and sort of moving from place to place on the bushings. I did preheat here also like I did on the boom. In the end, I could still slide the shaft between the bushings.
Certainly unconventional, but I think it worked ok. Best of all - on budget!. lol
The fab shop hasn't gotten to my plates yet, so nothing new on the quick attach plate.
Last edited: