alaskaforby4
Senior Member
Today I "learned" alot! haha. I had big plans of ordering some annular cutters and broaches and all sorts of stuff. Then all of a sudden its project time. So I have a set of dewalt cobalt bits up to 1/2" and a chinese set up to 1". There sure is something to be said about quality products.
My question is, what is the recomended drill bit step size? We were doing 9/16 to 1/2 to 13/16 to 1" The 1" bit was completly shot and we only managed to get one complete hole drilled all day! We got everything pre-drilled to 1/2 and 13/16" but by the end of the day the bits were ground to nubs. Which brings me to the second thing I learned about, Drillbit sharpening. There is alot that goes into that, have alot to learn there. Sometimes I could get a really good on and it would eat it up like butter, but could rarely duplicate it. Lots to learn! I'm planning on going to town next week to get some proper bits


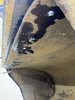
My question is, what is the recomended drill bit step size? We were doing 9/16 to 1/2 to 13/16 to 1" The 1" bit was completly shot and we only managed to get one complete hole drilled all day! We got everything pre-drilled to 1/2 and 13/16" but by the end of the day the bits were ground to nubs. Which brings me to the second thing I learned about, Drillbit sharpening. There is alot that goes into that, have alot to learn there. Sometimes I could get a really good on and it would eat it up like butter, but could rarely duplicate it. Lots to learn! I'm planning on going to town next week to get some proper bits



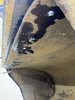