John C.
Senior Member
Summary Case study; Excavator was overloading the engine once in awhile. No fault codes. Some troubleshooting done and adjustments made to lessen the problem. A week later the problem got worse. Troubleshooting included checking pressures on both main and load sense circuits, pulling suspect screens in the control passages in the valve and pump controls. Proper load sense pressure was getting back to the pump. Rear pump seemed to be "hanging on stroke" so the end caps were pulled and the servo piston had to be hit with something to move it. The pump was removed from the machine and the rear section disassemble to check. The following photos show what was found.

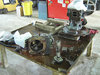
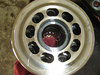
