How the hell did this thread go from a problem on a BCIII follower/cam to a small cam magnum that cummins only produced in 87. There was a reason the small cams
were discontinued and big cams arrived on the seen. But even that has no bearing on Hallback's problem.
Truck Shop,
The reason for Magnum was so Cummins could get rid of small cam engine cores. petepilot, myself DIY Magnums preceded Cummins; not brain science just using BC parts on small cam engines. Also work with NTC335s, non aftercooled for 400Hp, narrow nose Pete butter-fly hood type.
Cummins camshafts/roller followers regardless of Small Cam, Big Cam
do have a bearing on Hallback's problem. ALL share a common failure mode; failures by sloppy/wrong adjustment procedures.
ALL share a remedy to help prolong cam service life; i.e. retarding timing and using lower pressure high flow injectors, PT pumps with lower pressure.
Prolonging liner-ledge service life is also a benefit of using retarded injector timing. My reason for including KW#2 example; timing new per CPL spec 0.0325"-0.036", per 1st in-frame 0.046", per 2nd in-frame 0.056"
Advanced timing rattles liners, wearing liner ledges. Retarded timing is like a slow hard push; per dyno tests = increased torque/hp, per off-road torque converter equipment specification, engine using PTR pumps. Also per driver's seat of pants, pulls like a tractor; i.e. increased lugging power.
FYI crowned roller followers and cam lobes are not a 'silly idea' but based upon sound engineer design. Follower rollers are crowned to prevent edge loading; steel
deformed under load ditto camshafts. Crowning is used by most major OEMs, high-perf off road, aircraft engines.
ADT AR855 Stainless Pulsed Manifold
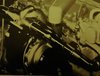
Designed by James J. Fueling and Garry Shidner, patented reverse flow flange design, mileage increase 0.7th. Cummins changed exhaust port design; smaller increasing velocity; i.e. killed the AR855 manifold
Hallback's BCIII cyl-block if produced after Sept 87 has increased upper deck thickness, 1.0" to use LPF liners.
LPF liners were a design carry over from KT-series engines.
Advantages of
LPF liners
1) the liner press fit is increased over the circumference area [more sq-inches]
2) held more securely lower in the block [approx 3/8” lower]
3) being held more securely in the block helps eliminate seeping head gaskets [increased support reduces liner movement @ circumference-liner ledge and ledge to top of counterbore]
4) extends liner-ledge service life [increased liner support lower in cyl-block with increased surface area]
5) helps eliminate cavitation corrosion-pitting caused by liner movement [combustion forces cause expansion-contraction, bubbles > cavitation corrosion-pitting]
6) reduces ring-blow-by [reduced cylinder distortion > caused by combustion forces; piston compression ring moved upwards > improved liner support in the highest cylinder pressure areas @ TDC]
7) helps prevent head bolt thread cracking [lots of cracked threads are mechanic’s error; i.e. did not clean out coolant-oil before installing the head, causes hydraulic pressure cracking]
note; 4) above: Cummins-Cat use/recommend using a stainless shim allowing polishing-wear to occur to the shim, instead of liner ledge wear
note; 6) above: emissions > combustion gases trapped between the upper compression ring-cylinder wall increase No2.
Hopefully Hallback can connect dots and question whomever repairs his retire-toy truck if he doesn't do the engine repairs himself.