I'd slap a freshman if he came out with a statement like that especially in front of a customer or in public..
They will be used to apply a gently metered force to realign the misaligned lifting structure from the awd skid steer.....to with in an appreciable tolerance to assure realignment of all the pivot points.this structure will then be checked for additional work, stress fractures etc prior to you; the customer making a lubain of it again..
................might need to review them certificates and Diplomas............................................ maybe it time for a refresher ....
LoL...Stock, once again, your skills as a wordsmith is a pleasure to read. :notworthy
Tigerotor, I took a few pics (actually, quite a few) of the area of failure, I'll try to post the ones that give the best views of how the failure progressed.
This first pic shows the way to pin boss would have been oriented. The side plates have been cut away and what remains is the top and bottom web members. Now, keep in mind, the side plates are an important part of the assembly, but they can't hold the pulling load that is on the assembly because they're only 3/16" thick steel. The critical part that bears the pulling load between pin boss and loader arms is the welds that attach the pin boss to the top and bottom web members, they are 2" wide / 1/2" thick steel. The top web member weld is where the original crack developed. Once the weld cracked entirely, now the pulling load was transferred to the side plates as they encircle the pin boss. The right plate cracked next, then all that was left holding was the left plate. There's no way the left plate could hold the load by itself, so it would have rapidly pulled apart. Once the entire top frame members failed, it would have simply peeled away from the top breaking the bottom web member weld and tearing the bottom circle of the side plates. Pretty much done then.
This pic shows what it would have done once the top attachment failed. It pulled away and bent the bottom web member downward. Then the pin boss would have rolled backwards and tore off the lower circle of the side plates. If you look closely at the side plate that is still attached to the pin boss, down at the bottom of pin boss, you can see the steel of the side plate is bent downward from the pin boss rolling counterclockwise then tearing the steel of the side plate. This is the obvious clue that the top failed first and left the bottom to hold the load.
This is the top weld. Notice the rust on the weld that attached the pin boss to the top web member. Rust indicates that a fracture has been there for a period of time. Notice also, there is no rust where the side plate broke on the left, but there is rust on the right side plate. This indicates the weld was cracked, and that it extended to the right side plate. But notice at the very bottom of the right plate, there is a (seemingly) tiny portion of the right side plate that is rust free. This means the left plate and that tiny piece of right plate was all that was holding the pulling load. Once that little piece of right plate let go, the left plate wouldn't have lasted long, and it all came unwound.
Another thing that is noteworthy of the top weld is the right side of the weld, it was only about a 1/4" thick. This in an area of attachment to a 1/2" thick plate. It appears in production, Bobcat only gives this joint a single pass of weld. And this one didn't even cover the full 1/2" of the web member.
Here's looking at the top web member. Sure didn't get a full weld in there did they.
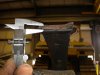