BrianGrenier
Senior Member
On the old road grader I have mocked-up a couple of 12"x2" trailer receiver tubing, 1/4" alloy steel, that will accept a pair of mounts connected to my new (old) 10' snowplow.
What I am wondering is, can I maybe get satisfactory welds with my Lincoln 100hd using .035 wireflux core with preheat?
I'm planning on getting all the paint off, then preheat with the torch. The frame of the blade is 1.5" and thicker at the corners.
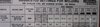
What I am wondering is, can I maybe get satisfactory welds with my Lincoln 100hd using .035 wireflux core with preheat?
I'm planning on getting all the paint off, then preheat with the torch. The frame of the blade is 1.5" and thicker at the corners.
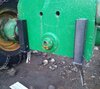
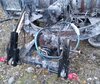
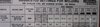