kshansen
Senior Member
- Joined
- Mar 11, 2012
- Messages
- 11,165
- Location
- Central New York, USA
- Occupation
- Retired Mechanic in Stone Quarry
The solenoid should be part number 4V1222. Circled in red below"
I always found it easier to remove and install by removing the nut that is in the center of that tag with the numbers on it and slide the coil with the two wire terminals off then use a large socket to unscrew the part from the valve body. As I recall that 45º elbow just above it in picture is in the way of the wire terminals. Plus the hex at the bottom of the valve is so thin it's hard to get a wrench on good.
Also right where the "F" is located in that picture would be where the control cable from the cab control lever would come out of the top of the valve. The small red arrow points to the bolt you need to remove to get the cable to slide out of the valve body.
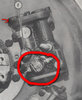
I always found it easier to remove and install by removing the nut that is in the center of that tag with the numbers on it and slide the coil with the two wire terminals off then use a large socket to unscrew the part from the valve body. As I recall that 45º elbow just above it in picture is in the way of the wire terminals. Plus the hex at the bottom of the valve is so thin it's hard to get a wrench on good.
Also right where the "F" is located in that picture would be where the control cable from the cab control lever would come out of the top of the valve. The small red arrow points to the bolt you need to remove to get the cable to slide out of the valve body.