Chrisso
Senior Member
730, 3F3 prefix w/ payload fitted from factory.
So the problem was an active 6863- 9 Payload Weight #1 : Abnormal Update Rate code.
Played looksies and swapsies, identified the #1 payload sensor has failed internally.
It shouldn't have, because all literature for this code alludes to there being a communication error between ECMs and or a data link error, but anyway...
I would like to know how these systems calculate weight. There are 2 accelerometers (front & rear) and 8 x 550-0975 Strain Sensors (4 on each side). What the heck is a strain sensor?
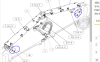
So the problem was an active 6863- 9 Payload Weight #1 : Abnormal Update Rate code.
Played looksies and swapsies, identified the #1 payload sensor has failed internally.
It shouldn't have, because all literature for this code alludes to there being a communication error between ECMs and or a data link error, but anyway...
I would like to know how these systems calculate weight. There are 2 accelerometers (front & rear) and 8 x 550-0975 Strain Sensors (4 on each side). What the heck is a strain sensor?
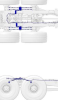
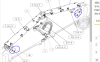