Tugger2
Senior Member
This technique of doing a small weld fill on the run out ends worked well for me on reinforcing plates and thumb mount bases. We would gring and polish the ends of the weld without digging into the base metal. I always used plug welds ,oval or round in the centre of the boom with assumtion you were welding in the neutral axis of the box. The idea came to me from the method Hitachi used on Cyl lugs and reinforcing cover plates. We cut up brand new machines and made them into high walker log loaders,back in the days of UH16 s and 181s. John deere guys came to our shop and said it wouldnt work so well. Look at them now. All that said i would not be afraid of repairing that Case boom.Ive repaired much worse when loggers i worked for started road building with 245 Cats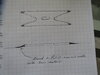
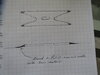