Birdseye
Well-Known Member
Now that cold weather and hard starting season is here for myself and many of us, I’d like to hear others opinions about good battery cables and ends.
So as not to waste time and money what’s the best way to improve or repair battery cable ends ?
The McMaster-carr catalog lists the following battery cables and end types:
—factory made cables new cables—-
..or repair existing cables with
—-Lugs for a threaded post—
crimp on lugs, needs crimper
Solder filled lugs
lugs with compression nut
..or
——-clamps——-
crimp on clamps
Solder&flux loaded clamps
Two bolt squeeze down clamp (probably the worst choice)
Compression clamps
https://www.mcmaster.com/battery-terminal-lugs/
Any opinions about what works and what doesn’t?
Thanks !
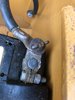
So as not to waste time and money what’s the best way to improve or repair battery cable ends ?
The McMaster-carr catalog lists the following battery cables and end types:
—factory made cables new cables—-
..or repair existing cables with
—-Lugs for a threaded post—
crimp on lugs, needs crimper
Solder filled lugs
lugs with compression nut
..or
——-clamps——-
crimp on clamps
Solder&flux loaded clamps
Two bolt squeeze down clamp (probably the worst choice)
Compression clamps
https://www.mcmaster.com/battery-terminal-lugs/
Any opinions about what works and what doesn’t?
Thanks !
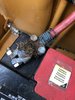
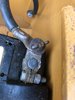