NH575E
Senior Member
This is my Titan 36" weld on thumb install:
This did not come with instructions and I'm not saying this is the right way to install one but its how I did it and it seems to work okay.
First off my welding is limited by lack of skill and equipment. My welder at home is a Lincoln SP100 mig. I was doing this outside with a light breeze which isn't the best conditions. I turned the heat all the way up, set my wire feed at 4, and cranked the shielding gas up to 28 CFM. Each weld required 3 or 4 passes starting as deep in the groove as I could get and working my way out. This little 100 amp welder has a 20% duty cycle so I have to weld a couple of minutes then let it cool for 8 or 10. Takes patience but it gets the job done.
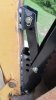
To set it up I curled the bucket all the way in and pulled the dipstick in to a point I could rest it. I assembled the thumb components and set it on the boom resting against the bucket. I set the stow bracket so the thumb was in contact with the bucket teeth. This had an unplanned benefit in that when I went to stow it after use I could curl the bucket all the way in and the support arm holes were in alignment with the stow bracket. Of course I had to set it up and mark the location where I needed to grind off the paint then set it up again to weld.
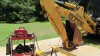

The support arm was rounded on one side but they left the back side flat. Either way I installed it would bind before the holes lined up so I had to grind the ends so they were rounded on both sides. The length of the support arm isn't long enough to set the thumb a full 90 degrees. I was hoping to be able to set it slightly forward but that isn't possible with the supplied support.

This is one heavy hunk of metal for the price of $215 shipped. The thumb has 5/8" sides with 1/2" front and back plates. The mounting and stow brackets are formed 1/2" u channel. The support arm is made from 3/4" sides with 1/2" front and back plates. It won't be anywhere near as handy as a hydraulic thumb but will be much better than no thumb at all. It could be converted to hydraulic but the cost isn't in my budget right now.
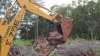
This did not come with instructions and I'm not saying this is the right way to install one but its how I did it and it seems to work okay.
First off my welding is limited by lack of skill and equipment. My welder at home is a Lincoln SP100 mig. I was doing this outside with a light breeze which isn't the best conditions. I turned the heat all the way up, set my wire feed at 4, and cranked the shielding gas up to 28 CFM. Each weld required 3 or 4 passes starting as deep in the groove as I could get and working my way out. This little 100 amp welder has a 20% duty cycle so I have to weld a couple of minutes then let it cool for 8 or 10. Takes patience but it gets the job done.
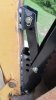
To set it up I curled the bucket all the way in and pulled the dipstick in to a point I could rest it. I assembled the thumb components and set it on the boom resting against the bucket. I set the stow bracket so the thumb was in contact with the bucket teeth. This had an unplanned benefit in that when I went to stow it after use I could curl the bucket all the way in and the support arm holes were in alignment with the stow bracket. Of course I had to set it up and mark the location where I needed to grind off the paint then set it up again to weld.
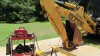

The support arm was rounded on one side but they left the back side flat. Either way I installed it would bind before the holes lined up so I had to grind the ends so they were rounded on both sides. The length of the support arm isn't long enough to set the thumb a full 90 degrees. I was hoping to be able to set it slightly forward but that isn't possible with the supplied support.

This is one heavy hunk of metal for the price of $215 shipped. The thumb has 5/8" sides with 1/2" front and back plates. The mounting and stow brackets are formed 1/2" u channel. The support arm is made from 3/4" sides with 1/2" front and back plates. It won't be anywhere near as handy as a hydraulic thumb but will be much better than no thumb at all. It could be converted to hydraulic but the cost isn't in my budget right now.
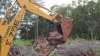