1693TA
Senior Member
Decided to start and new thread rather than continue to cabbage onto Aighead's.
Got a call from guys with the manlift and they were done with it. Said they noticed a slight leak as the machine got warmed up. Back at the shop I found a 3/8" hose rubbed through from slight movement as the boom elevates. I replaced the same and then rode the basket up and down twice to purge air from this circuit operating the basket swivel each way several times at elevation, and ground level. I then went to the top again and at the extreme end of travel for the boom lift cylinder. I heard the relief valve function and a "Pop"! along with an immediate spray of oil. Blew the main hose for the boom lift cylinder. Safeties worked as they should and boom did not shudder, or drop at all with the sudden loss of hydraulic pressure. However driving the boom back down so I could get out made a real mess of oil. I grabbed a clean, large drain pan and was able to probably capture about half of what evacuated the system so it will be strained, filtered, and reused till a complete change out later this year.
I coupled "Fred" to the boom and using the combination of his winch power, weight, and limited hydraulic pressure available though the boom lift circuit, was able to get the boom back to where I can work on replacing the blown hose which is in the center pedestal.
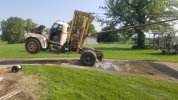

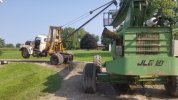
I've since relaxed "Freds" winch tension and the boom is held in placed with it's counterbalance valve. The photos do not show the current elevation of the boom which is about parallel to the ground.
All that steam cleaning last week to finally be rid of the greasy mess this lift has been for years.....
Got a call from guys with the manlift and they were done with it. Said they noticed a slight leak as the machine got warmed up. Back at the shop I found a 3/8" hose rubbed through from slight movement as the boom elevates. I replaced the same and then rode the basket up and down twice to purge air from this circuit operating the basket swivel each way several times at elevation, and ground level. I then went to the top again and at the extreme end of travel for the boom lift cylinder. I heard the relief valve function and a "Pop"! along with an immediate spray of oil. Blew the main hose for the boom lift cylinder. Safeties worked as they should and boom did not shudder, or drop at all with the sudden loss of hydraulic pressure. However driving the boom back down so I could get out made a real mess of oil. I grabbed a clean, large drain pan and was able to probably capture about half of what evacuated the system so it will be strained, filtered, and reused till a complete change out later this year.
I coupled "Fred" to the boom and using the combination of his winch power, weight, and limited hydraulic pressure available though the boom lift circuit, was able to get the boom back to where I can work on replacing the blown hose which is in the center pedestal.
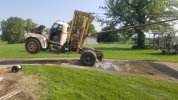

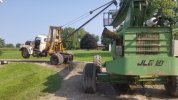
I've since relaxed "Freds" winch tension and the boom is held in placed with it's counterbalance valve. The photos do not show the current elevation of the boom which is about parallel to the ground.
All that steam cleaning last week to finally be rid of the greasy mess this lift has been for years.....