willie59
Administrator
Ok all you wrench benders, this is a shop forum, let's see the tools and gagets you work with to get something done. There's a lot of small owner/operators/repaimen on this forum that I'm certain would like to see "a better way" to get a task accomplished. I think I've posted these pics somewhere buryed in the forum sections, beats me where the heck they are though, so I thought a designated tools thread would be a good reference place for the useful shop tools that we work with.
This is a tool that's as handy as a handle on a shovel head. A hollow ram Enerpace hyd cylinder. This one goes for around $850 to $1000 retail depending on where you look, I scored this one on ebay for $375 + shipping, no regrets spending that money for this tool. You can use it as a typical pushing jack cylinder like other porta power cylinders, but you can also insert up to a 1 1/4" rod through it to perform pulling tasks. It's handy for removing and install bushings in cylinder rod ends for example. Very handy shop tool, have used it on many occasions.
I've got it set up here to remove and install rubber isolater bushing inserts on a Case Maxi-Sneaker vibratory plow. Ever tried to remove or install compressed rubber inserts with a hammer? Good luck with that! With this tool, piece of cake. Here's the removing set up with a pushing sleeve on backside of the insert.

Tighten the nuts on the threaded rod until pushing sleeve is against the steel bushing in center or rubber insert,

Then simply pump the cylinder.
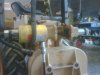
Bushing removed slicker than snot on a door knob.

Re-installed new bushings by greasing everything with silicone lube, fitted new bushing on backside of square tubing socket, fitted up the pulling rod and simply pulled the new isolater in place. I've used this tool to install bushings on loader arms, excavator bucket pin bushings, all kinds of tasks I used to do with a sledge. I'd rather use this tool as opposed to a sledge anyday.
This is a tool that's as handy as a handle on a shovel head. A hollow ram Enerpace hyd cylinder. This one goes for around $850 to $1000 retail depending on where you look, I scored this one on ebay for $375 + shipping, no regrets spending that money for this tool. You can use it as a typical pushing jack cylinder like other porta power cylinders, but you can also insert up to a 1 1/4" rod through it to perform pulling tasks. It's handy for removing and install bushings in cylinder rod ends for example. Very handy shop tool, have used it on many occasions.
I've got it set up here to remove and install rubber isolater bushing inserts on a Case Maxi-Sneaker vibratory plow. Ever tried to remove or install compressed rubber inserts with a hammer? Good luck with that! With this tool, piece of cake. Here's the removing set up with a pushing sleeve on backside of the insert.

Tighten the nuts on the threaded rod until pushing sleeve is against the steel bushing in center or rubber insert,

Then simply pump the cylinder.
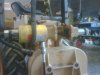
Bushing removed slicker than snot on a door knob.

Re-installed new bushings by greasing everything with silicone lube, fitted new bushing on backside of square tubing socket, fitted up the pulling rod and simply pulled the new isolater in place. I've used this tool to install bushings on loader arms, excavator bucket pin bushings, all kinds of tasks I used to do with a sledge. I'd rather use this tool as opposed to a sledge anyday.