Swetz
Senior Member


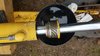
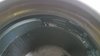
I was finally able to tear down the stabilizer cylinder that has been leaking on the NH675E that I recently purchased. I figured I would share my experience with others on this site. Obviously, many do not need a how too, but others can learn a lot, as I have from the many posts I have read.
So, I finally go a break from the rain on Friday afternoon, and Saturday was forecast not to rain (just for the record, we are back in rain today), so I jumped on the repair. First, I removed the pin. In order to remove the pin, you need some pliers that are made for the flat style snap ring (see the pic.). Then the pin is then driven out...make sure that you do not mushroom the pin or it will not come out. To drive the pin out I used a round drift (see pic.), and held it in place with a pair of vice grips as not to get hit by the hammer. Make sure that your drift is not hardened steel or injury could result! Once the pin is out, support the barrel of the cylinder (I used a 6x6 and rubber chock (see pic). At this point the gland nut is removed. To aid in loosening the gland nut, use a large ball peen hammer and start near the gland and hammer in a strait line, in several spots (see the marks on the cylinder). To loosen the gland nut you will need a specialized tool. I used an OTC adjustable spanner that I modified with 7/16" pins as the ones supplied were a bit small for the holes in the gland nut. Other brands are available at lower cost, but I cannot tell you if the holes are 7/16" as mine were. I used a 3/4" breaker bar on the OTC tool to break the nut loose. Once it was loose, I used a 3/4" to 1/2" adapter and a half inch ratchet to finish the job. At this point you need to make sure that you have a drain pan in place, because when the gland comes out, the oil will also come out. I used a 5 gallon pail that I cut the top off of so it would fit, it worked great. I then loosened (not remove) the hydraulic supply and return lines. Only the extend hose has to be loosened in order to get the piston out, but you will need to loosen the retract to get the cylinder back together, so why not loosen both now. Now the piston can be pulled out. Again, be careful just before the head comes out as the rest of the oil will come out. Once the cylinder rod assembly is out, you must now remove the piston from the rod. My application had a bolt that was 1 13/16" (45MM). To loosen this bolt, you put the pin on the stabilizer that you previously removed (be sure that you keep the rod out of the dirt). This will hold the rod from turning as you loosen the bolt. To break the bolt, I used the 36" 3/4" drive breaker bar with a piece of pipe slid over the handle for leverage. Once loose, I used an adapter and a 1/2" impact gun to remove the bolt (be sure to note the orientation of the piston). Once the bolt is out, the gland can be slid off the rod. I took the gland and piston into my work area for the seal replacement. First, I cleaned the gland and removed the seals (note the orientation of the seals, they will not work is put in backwards). My seals were just falling apart. To remove the wiper seal, I used an old screwdriver that had 1 side of the tip ground and the other left flat. This would allow the blade to get under the seal the start it out. I then used a large screwdriver and twisted the handle to remove the seal. I used some cheapo harbor freight picks to remove the seals inside the gland. For the wear ring, I used a small screwdriver to start, then some needle nosed pliers in a twisting motion. To install the seal in the gland I used a seal installation tool that I purchased on ebay for less than $30. This makes quick work of the seal installation. The seal can be installed without this tool but for $30 bucks it is well worth it. The wiper is press fit, I used a hammer to tap the seal in...be sure to keep the seal square as you hit it in. While you are doing this work on the gland is a good time to put the new piston seal in some hot water. The last part to be replaced is the o-ring and backer on the outside of the gland. Be sure to note the the positioning of the o-ring and backer before removing. Now that the gland is finished, it is time to replace the seal and backer. The old seal can be removed with a pick. Then the backer is removed in the same manner. The new backer is installed using a pick (be sure not to stick the pick into the material). Now the hot seal is installed. I again use the pick being careful not to damage the seal. The seal will stretch a bit while being installed. This is ok, and the seal will somewhat contract on its own. I like to use an old wear ring wrapped around the seal with a worm gear clamp to compress the seal. If you have an automotive ring compressor that will work too. Leave that to sit while you check the inside of the cylinder to make sure it is in good condition. If you suspect gouging be sure to check this early on, so you do not waste time with the rebuild. I like to use a flash light to look down the barrel. It should be shiny all the way around. I use brake parts cleaner to get the residual oil out of the barrel and clean it up. Now it is time to slide the gland back on the rod (be careful of orientation or you will need to take it back apart). To put the gland on, oil it first and install by pushing and twisting at the same time. There is a chamafer (lead) on the end of the rod that is there to help. Once the gland is on the rod, the the piston assy. can be installed (note orientation). I ran the bolt up with a 1/2" impact then tightened with a 3/4" drive breaker bar and a pipe. Now the piston is ready to be installed...take what ever you used to compress the seal, lube the piston, and insert in the barrel. I install with a push/twisting motion like used for the gland. I have a large prybar that I install in the eye of the rod to help with the twisting motion...be sure to wiggle the rod a bit too. There is a lead on the end of the barrel that is helping you compress the seal as the piston goes in (this is where the extend hose MUST be loose so that air can escape). Once the seal is in the piston should slide in relatively easily. I usually slide the rod about 1/2 way in the barrel. At this point I lube the seals on the gland. I also use never-sieze on the threaded part. I then carefully slide the gland in and start it by hand. I thread in by hand as fr as possible, then use the 1/2" ratchet until it needs more force. I finished off with the 3/4" drive breaker bar. Don't forget to tighten the hoses...this is a good time to do this. Now the pin is installed in the stabilizer foot. I clean the pin on a wire wheel and fit test it first, It should slide in smooth and easy. I then line up the rod and start the pin in the first ear. I then put lube on the pin, and never sieze in the second ear. I push the pin 3/4 of the way in and put never-sieze on the pin that has not yet been installed (now both ears will have never-sieze in them). Don't forget the washers, and install the lock ring. Test the cylinder by running it in and out several times...this will also purge the air. Place the the unit in the manufacturers recomendation, and check/top the oil...Crack a beer!!