I found a pic. of a Case pin that shows the recess I was talking about. Click on the 2nd pic.
https://www.minnpar.com/product.asp?PartNbr=105752A1&StockNbr=QR6881820&ProductCode=550901
I get what you're saying, but IMO there's a difference between the function of the two piins. The type of pin in your photo is being pretty much entriely held against rotation by the weld on the flag (locking plate) with very little in the way of side to side forces being applied to it.
Also the plate to which the pin is being welded is not that thick. If the pin was left shy of the outside by even a 1/4" it would IMO increase the bending moment on the plate significantly.
The pin in that 939C Tilt Link has to be held against both rotational and significant side-to-side forces because of the loose plate #12 on the outdie of the assembly. That's why I suggested an interference fit of both pins into the lever. Also having an interference fit between the pin and the plate will IMO largely stop the pin from moving while it is being welded and help to maintain alignment.
For correct alignment it would be necessary to assemble everything with both the inside (fixed) and outside (loose) plates in position then weld the end of the pins to the plate. At each stage of the welding the outside plate could be checked to ensure that it was still free to move on the pins.
Here's another thought. Are both the inside and outside plates still true (straight in other words)..?
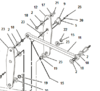