The blade skin on my D6c was paper thin when I got it several years ago. I've put a few small patches on it and welded up some cracks but after this fall I figured it was time to do a re-skin.....more areas cracking and so thin it's hard to weld on a patch.
There is a local shop that has a large plate roller they use all the time and they quoted a 3/8" x 4' x 10' AR400 plate for $550 plus $225 to roll it.
I may end up getting a 5' x 10' sheet and have them roll it the narrow direction and cut it into two sections to make it a little easier to handle.....that will cost a little more for material. Sounds like a pretty reasonable price.
Here's the problem.....
I cut off the center push plate that was 3/8" and found the skin worn through underneath....no problem except there is another skin under that. I suspected it had been re-skinned before because of the way the top edge welds look but didn't know if they had removed the old skin first.....guess not.

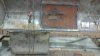

On the left side of the blade about 1/3 of the way up the outside skin was dished in. (see first pic) To see what was there I torched a hole in the skin and found in that area there isn't any skin underneath. Looks as though someone torched out a section of the original skin in that area before overlaying the new skin.
It's kind of a mess.....I found about 2" of wet sandy mud inside the blade where the lower part is boxed. The way the other side looks it may well be in similar shape.
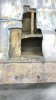
So....do I go ahead and torch off both layers of skin and start over or is it time to find another blade? Not long ago I replaced the trunnion balls on the blade corners and welded in new trunnion bearings in the front of the push arms. I've also tightened up the other pin holes for the braces, so except for the skin it's in pretty good shape.
I do know where there is a used dozer from a D6c.....don't know the price yet, but he did say the blade face was pretty good but it was a little loose in the pins, etc.
Might end up with quite a bit of work fixing up a used dozer blade if I went that route.
What would you do?
There is a local shop that has a large plate roller they use all the time and they quoted a 3/8" x 4' x 10' AR400 plate for $550 plus $225 to roll it.
I may end up getting a 5' x 10' sheet and have them roll it the narrow direction and cut it into two sections to make it a little easier to handle.....that will cost a little more for material. Sounds like a pretty reasonable price.
Here's the problem.....
I cut off the center push plate that was 3/8" and found the skin worn through underneath....no problem except there is another skin under that. I suspected it had been re-skinned before because of the way the top edge welds look but didn't know if they had removed the old skin first.....guess not.

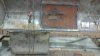

On the left side of the blade about 1/3 of the way up the outside skin was dished in. (see first pic) To see what was there I torched a hole in the skin and found in that area there isn't any skin underneath. Looks as though someone torched out a section of the original skin in that area before overlaying the new skin.
It's kind of a mess.....I found about 2" of wet sandy mud inside the blade where the lower part is boxed. The way the other side looks it may well be in similar shape.
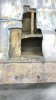
So....do I go ahead and torch off both layers of skin and start over or is it time to find another blade? Not long ago I replaced the trunnion balls on the blade corners and welded in new trunnion bearings in the front of the push arms. I've also tightened up the other pin holes for the braces, so except for the skin it's in pretty good shape.
I do know where there is a used dozer from a D6c.....don't know the price yet, but he did say the blade face was pretty good but it was a little loose in the pins, etc.
Might end up with quite a bit of work fixing up a used dozer blade if I went that route.
What would you do?