CraneInnovation
Well-Known Member
I have been working on rebuilding a 1988 Gradall G3WD and have made a few puzzling discoveries on the hydraulics system. I have a thread going in the Shop Talk forum about the rebuilding project:
https://www.heavyequipmentforums.com/showthread.php?38100-The-Great-Gradall-Project
..but I wanted to get some thoughts from the Excavator forum about what I found.
On the factory machines, one output from the tandem pump on the G3WD goes straight to the center pin while the other goes to a valve on the frame that powers the remote travel motor (to allow carrier driving from the excavator cab). If the fluid is not used by that valve, it goes through a power beyond port and joins the other line at the center pin. All parts and service manuals agree that this is the ONLY circuit that Gradall ever put on these machines after the main pump. The main pump is mounted to the torque converter just behind the engine.
I have the 4x4 version where the transmission is mounted at mid-ship and is not supposed to have anything connected to its PTO.
Here's what I've found on my machine.
Our first discovery was two high pressure filters near the main pump.
One is currently bypassed:
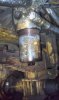
The other one is plumbed just after the second main pump output:

We haven't traced the lines in full, but it doesn't appear that that second filter output goes to the remote travel valve. The first pump output goes directly to the center pin through a hose that is zip-tied to the frame. So yeah, someone's been busy making it "better".
The other thing we discovered this weekend was a total surprise. There is a second single stage hydraulic pump on the transmission PTO:


It appears (without confirmation, we discovered it at 9pm on Saturday after replacing the TC charge pump) that this pump comes directly after the smaller high pressure filter. This would mean that it comes AFTER the main pump. Huh???
The G3WD is a low pressure machine (~2000psi and the last one Gradall built before going high pressure on the 4100) and a booster pump might make sense? I don't know enough about hydraulic system modifications to know if that is ever "done". I am new to hydraulics servicing and the only thing I'm sure of is that this is all after-market (Gradall has confirmed none of this was shipped with any of their machines). Granted, there IS a PTO on the transmission so its not a bad idea...
In summary, my question to everyone is this: Has anyone ever seen these kinds of after-market modifications before? If so, what was their purpose? Is there any value in keeping them or should I restore the machine to its original configuration?
(We are completely disassembling and rebuilding all hydraulics....so I am wondering if it is worthwhile to include this stuff in the rebuild or to remove it?)
Thanks so much for any pointers. Like I said, this is a new ball of wax for me!
https://www.heavyequipmentforums.com/showthread.php?38100-The-Great-Gradall-Project
..but I wanted to get some thoughts from the Excavator forum about what I found.
On the factory machines, one output from the tandem pump on the G3WD goes straight to the center pin while the other goes to a valve on the frame that powers the remote travel motor (to allow carrier driving from the excavator cab). If the fluid is not used by that valve, it goes through a power beyond port and joins the other line at the center pin. All parts and service manuals agree that this is the ONLY circuit that Gradall ever put on these machines after the main pump. The main pump is mounted to the torque converter just behind the engine.
I have the 4x4 version where the transmission is mounted at mid-ship and is not supposed to have anything connected to its PTO.
Here's what I've found on my machine.
Our first discovery was two high pressure filters near the main pump.
One is currently bypassed:
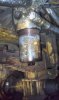
The other one is plumbed just after the second main pump output:

We haven't traced the lines in full, but it doesn't appear that that second filter output goes to the remote travel valve. The first pump output goes directly to the center pin through a hose that is zip-tied to the frame. So yeah, someone's been busy making it "better".
The other thing we discovered this weekend was a total surprise. There is a second single stage hydraulic pump on the transmission PTO:


It appears (without confirmation, we discovered it at 9pm on Saturday after replacing the TC charge pump) that this pump comes directly after the smaller high pressure filter. This would mean that it comes AFTER the main pump. Huh???
The G3WD is a low pressure machine (~2000psi and the last one Gradall built before going high pressure on the 4100) and a booster pump might make sense? I don't know enough about hydraulic system modifications to know if that is ever "done". I am new to hydraulics servicing and the only thing I'm sure of is that this is all after-market (Gradall has confirmed none of this was shipped with any of their machines). Granted, there IS a PTO on the transmission so its not a bad idea...
In summary, my question to everyone is this: Has anyone ever seen these kinds of after-market modifications before? If so, what was their purpose? Is there any value in keeping them or should I restore the machine to its original configuration?
(We are completely disassembling and rebuilding all hydraulics....so I am wondering if it is worthwhile to include this stuff in the rebuild or to remove it?)
Thanks so much for any pointers. Like I said, this is a new ball of wax for me!
Last edited: