LACHAU
Senior Member
The pressure of the system depends simultaneously on all 03 relief valves A_B_C as shown below.
You must check; calibrate all three types of valves.
You should check and calibrate 02 relief valves A & B at the same time first.
If the pressure is still not reached, we will consider the relief valve C.
As MG2361 mentioned above, it is possible that your surge relief valve has been set to a low value. You should try increasing the pressure value of surge relief valve B to see how.

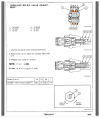
You must check; calibrate all three types of valves.
You should check and calibrate 02 relief valves A & B at the same time first.
If the pressure is still not reached, we will consider the relief valve C.
As MG2361 mentioned above, it is possible that your surge relief valve has been set to a low value. You should try increasing the pressure value of surge relief valve B to see how.

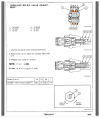
Last edited: