treemuncher
Senior Member
I looked up the correct tool for SKF's KM13 nuts so that I can properly change out my main rotor bearings on an FAE head. New bearings need proper preload and the proper tool for these was not in my inventory. A general spanner wrench can not get into the housing. Only a socket style tool with a deep throat will work. I did not have time and I did not want to spend the money on a new tool for 2 bearings that should last me until I retire out. Time to build another custom tool. This is why I save my old busted cheap Chinese sockets - they get repurposed rather than going into the scrap heap.
I already had 2 new nuts and locking washers to replace the old, gouged washers from previous chisel hits. I can make a good tool with one the better of the two old nuts. I looked up the dimensions of the nuts and the slots are 7mm - perfect for a piece of 7x7 key stock at $7 for a 12 inch piece at my local bearing house. I need the tool to have at least 4" throat depth.
Step one: Overbore the nut to remove the threads. Set final dimension to match shouldered piece of pipe for a press fit assembly.
Step 2: Cut 4 pieces of keystock just a little over twice the thickness of the nuts. Assemble a new nut with keystock against the old nut. Be sure the tapered edge faces in on the old nut and out on the new nut. Hold the assembly of nuts and keystock pieces together tightly with a properly sized hose clamp. Weld up the assembly at the pipe to old nut and old nut to keystock. I found the nuts are near impossible to weld with the MIG or 7018 rods - too much cratering and spatter - so I had to TIG weld with stainless rod and that was still difficult. Final product should look like this:
Step 3: Carefully grind down the keystock fingers to match the beveled edge of the new nut. Find an old, broken 3/4 drive socket and weld that in the center of the pipe for your tool drive. A nut would be another option for a drive part. Finished assembly should now look like this with a new nut still in the grip of the wrench.

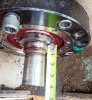
I already had 2 new nuts and locking washers to replace the old, gouged washers from previous chisel hits. I can make a good tool with one the better of the two old nuts. I looked up the dimensions of the nuts and the slots are 7mm - perfect for a piece of 7x7 key stock at $7 for a 12 inch piece at my local bearing house. I need the tool to have at least 4" throat depth.
Step one: Overbore the nut to remove the threads. Set final dimension to match shouldered piece of pipe for a press fit assembly.
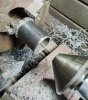
Step 2: Cut 4 pieces of keystock just a little over twice the thickness of the nuts. Assemble a new nut with keystock against the old nut. Be sure the tapered edge faces in on the old nut and out on the new nut. Hold the assembly of nuts and keystock pieces together tightly with a properly sized hose clamp. Weld up the assembly at the pipe to old nut and old nut to keystock. I found the nuts are near impossible to weld with the MIG or 7018 rods - too much cratering and spatter - so I had to TIG weld with stainless rod and that was still difficult. Final product should look like this:

Step 3: Carefully grind down the keystock fingers to match the beveled edge of the new nut. Find an old, broken 3/4 drive socket and weld that in the center of the pipe for your tool drive. A nut would be another option for a drive part. Finished assembly should now look like this with a new nut still in the grip of the wrench.
