Ronsii
Senior Member
- Joined
- Jun 26, 2011
- Messages
- 3,464
- Location
- Western Washington
- Occupation
- s/e Heavy equipment operator
when the rebar gets bad and circumstances allow, we have been running the aggressive diamond blades and cut it up in manageable pieces....diamond blades cost vs other costs and is more expedient and predictable. That job looks involved due to the size as well as other reasons. Did you have to change that channel? We always have a hard time with the handheldsaws on a wall horizontal cut and we dont have a wall saw - the saw specialists exact a toll on the wallet for their wall work
We had to do some cutting with the hand saw but just stuck with an abrasive blade, also had the 120 with a breaker on it for the majority of the work. I also used the breaker on the face of the wall 8" thick I think.... but what really slowed us down was the 5 filled in docklevelers you can probably see where they used to be in the pics, when someone put them in rebar must have been cheap because they used plenty... same with concrete it was well over a foot thick a their bases and a good foot thick all around the perimeter... and when they filled them in they used more rebar and filled solid with crete!!!
This was a complete demo so no changing the edge
I hear ya' on the saw guys, we sub a lot of wall and slab work out for door cuts on these tiltup's... have one of those stihl ts512 on the little walk behind cart I use for floor cuts up to a hundred or three feet it'll go 6 inches with the 16 inch blade on it but it's a lot slower then a real saw

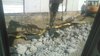
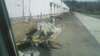
