Blueboy
Senior Member
- Joined
- Mar 14, 2015
- Messages
- 319
- Location
- pittsburgh Pa
- Occupation
- Machinist. God bless America ! ! !
I was going to post this in "shop talk" but since this is my usual hang out Ill post my question here.
I need to weld this hook onto the other side of this link. Both are cast steel.
I'm not a certified welder but I have a ton of hours in welding all kinds of material with all kinds of welders.
At home I will be using my old Lincoln 225A AC welder. I don't have an oven to keep the 7018 dry so I was leaning towards 7014. But it doesn't have the penetration of 6011.
So what is the advise from the experts?
Thanks! Blueboy

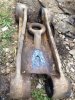
I need to weld this hook onto the other side of this link. Both are cast steel.
I'm not a certified welder but I have a ton of hours in welding all kinds of material with all kinds of welders.
At home I will be using my old Lincoln 225A AC welder. I don't have an oven to keep the 7018 dry so I was leaning towards 7014. But it doesn't have the penetration of 6011.
So what is the advise from the experts?
Thanks! Blueboy

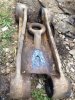