treemuncher
Senior Member
I've recently broken a plastic joystick on my Menzi Muck excavator. The parts were quoted at $173+ for each half of a plastic handle, not including any electronics or shipping from Switzerland. I also need some impossible to find switch covers that are "melting" from age or chemical reactions - quoted $85 - not sure if that's for one or all six. 
After recovering from a near cardiac moment from that quote, I started looking at 3D printers with carbon fiber media as a possible solution. Not really a cost effective approach for the few parts that I need to prototype or build and lots of computer time with CAD drawings. I would have to dredge up what I can remember from CAD and do a lot of relearning. Not the best option for me at close to $5k initial investment.
I then looked into custom casting with silicone molds and plastic resins. I could get into that for about the price of the joystick halves. For about $500, I could get enough tooling and supplies to get well underway and learn/perfect another skill. I enjoyed sand casting metals back in high school so I already had some basic knowledge of the process. Youtube is full of silicone mold videos so I watched enough to learn before I decided to make the plunge.
I already had a vacuum pump and compressor so for under $90, I purchased a pressure paint pot with spray gun that I needed anyways. I now have a pressure painter for big jobs, a pressure pot for resin casting and with the addition of a few fittings, a vacuum chamber for degassing silicones and resins. Xacto knife set at HF under $20, hot glue gun under $20, gallon silicone kit + 2 different hard plastics + 1 hard rubber plastic + modeling clay + mold release made up the balance of the budget and got me under way.
Starting small: These little button covers were getting soft whether from age or chemicals, I don't know, but they were melting/ripping and starting to fail. They were so bad that I had to make new patterns on the lathe. I could not find any plastic round stock so I cut the plastic patterns from the handle of an old screwdriver, made the center core from an old pencil, adjusted the depth of the center core to proper depth and then epoxied into place for the final patterns. I used an old cat food can as the mold container and poured up the mold in 2 halves with 2 buttons in the mold. I used the firm rubber texture resin to cast the buttons, cut the flashing off after curing and I have perfect replacement parts. I've now made 4 sets of castings from that mold and it works great. I have all new buttons when I get to put things back together.
Getting bigger: The joystick halves are much more complex. I had to glue the broken parts back together to make a good mold pattern. I also added modeling clay to the areas that I wanted to build up stronger with more material. I filled in the major gap with some aluminum ducting tape to provide a partition line. I cut out a tight fitting cardboard pattern to set my molding line and glued that with the hot glue. Built a mold box and then poured the first half of the mold. I did not degas this first silicone pour with the vacuum chamber and there is a noticeable difference from the later pour that was degassed for 5 minutes prior to pouring - the pressure pot is worth the difference in quality.
I still have to pour up the first joystick half and finish the mold of the second half. I will continue to edit and add to this post about results.

After recovering from a near cardiac moment from that quote, I started looking at 3D printers with carbon fiber media as a possible solution. Not really a cost effective approach for the few parts that I need to prototype or build and lots of computer time with CAD drawings. I would have to dredge up what I can remember from CAD and do a lot of relearning. Not the best option for me at close to $5k initial investment.
I then looked into custom casting with silicone molds and plastic resins. I could get into that for about the price of the joystick halves. For about $500, I could get enough tooling and supplies to get well underway and learn/perfect another skill. I enjoyed sand casting metals back in high school so I already had some basic knowledge of the process. Youtube is full of silicone mold videos so I watched enough to learn before I decided to make the plunge.
I already had a vacuum pump and compressor so for under $90, I purchased a pressure paint pot with spray gun that I needed anyways. I now have a pressure painter for big jobs, a pressure pot for resin casting and with the addition of a few fittings, a vacuum chamber for degassing silicones and resins. Xacto knife set at HF under $20, hot glue gun under $20, gallon silicone kit + 2 different hard plastics + 1 hard rubber plastic + modeling clay + mold release made up the balance of the budget and got me under way.
Starting small: These little button covers were getting soft whether from age or chemicals, I don't know, but they were melting/ripping and starting to fail. They were so bad that I had to make new patterns on the lathe. I could not find any plastic round stock so I cut the plastic patterns from the handle of an old screwdriver, made the center core from an old pencil, adjusted the depth of the center core to proper depth and then epoxied into place for the final patterns. I used an old cat food can as the mold container and poured up the mold in 2 halves with 2 buttons in the mold. I used the firm rubber texture resin to cast the buttons, cut the flashing off after curing and I have perfect replacement parts. I've now made 4 sets of castings from that mold and it works great. I have all new buttons when I get to put things back together.
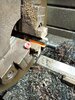

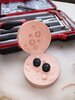
Getting bigger: The joystick halves are much more complex. I had to glue the broken parts back together to make a good mold pattern. I also added modeling clay to the areas that I wanted to build up stronger with more material. I filled in the major gap with some aluminum ducting tape to provide a partition line. I cut out a tight fitting cardboard pattern to set my molding line and glued that with the hot glue. Built a mold box and then poured the first half of the mold. I did not degas this first silicone pour with the vacuum chamber and there is a noticeable difference from the later pour that was degassed for 5 minutes prior to pouring - the pressure pot is worth the difference in quality.
I still have to pour up the first joystick half and finish the mold of the second half. I will continue to edit and add to this post about results.
Last edited: