621_Rocker
Well-Known Member
I have a small crack on two different 621 (A) scrapers that is nearly identical on each machine. The crack is on the cast section on the top of the differential/transmission housing. I spoke with my local Cat dealer about the metallurgy of this and they said that they did not know and that their welder would just do a spark test of the material. So far I have gotten the advice from other people to completely grind out the crack and then preheat the area (5"-6" surrounding but I have not been told what temperature range). Possibly use a UTP 62 rod and peen the weld. Do post heating and allow the area to cool slowly by insulating it with kitty litter. This is a very critical weld and I want to make sure that I do it right because the main force of the scraper weight comes down and is transferred around the drive line housing here. I want to have a strong weld and not weaken any of the existing structure. I have no experience in doing spark testing so I am not confident about using that test to determine my material. Does anyone of any knowledge of this or any more suggestions as far as preheat temperatures and rod to use? The arrow in the first photo is where the crack is and the second is of the crack.
621 Rocker
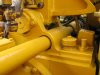

621 Rocker
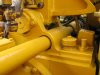
