Numbfingers
Well-Known Member
I'm sure this will start a lively discussion, but I wanted to get some input on a project for next year. I'm going to build a SMALL AND LEAN shop to house my service truck, some supplies, and all my other tooling that I don't carry on the truck daily. Also need some space to have a personal car project in there as well. The other reason for the shop is so I can for work on customer's components out of the weather. I don't do a whole lot of welding, so space for that was limited. I want to keep the welding area away from the waste oil and working area so I'm not throwing metal grindings and slag onto a customer's component. I will not be bringing machines into the shop, only an occasional component like an engine, axle, or pump, etc.. I'm building on a tight budget, out-of-pocket, so I'm not burdened with monthly payments. Take a look at my layout, and see if there's anything that could be done smarter based off of your experience. Kind of like the kitchen triangle you know? I already have the gravel pad done, and just waiting for spring(and more money). The dimensions are 32x40x14. 12x12 door on the short, gable side. I'm considering putting the man door on the left(boiler) side, and likely building a lean-to about 12' wide for storage. Anyways, your thoughts?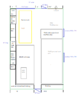
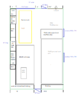