I have a 2016 New Holland 4.75 at work that came back with an engine miss. Figured it out to be bent pushrods. Full disclosure, my diesel repair experience has been very limited. I've rebuilt Ford and Chevy gas engines from scratch a number of times with no issues so I figured I'd give this a go.
I had to disassemble a lot of engine parts to be able to pull the valve cover off and took pictures along the way. All of the injectors had to come out and I kept everything in order so all injector components went back in the same spot they came from.
Replaced the pushrods and got everything back together and held my breath when I turned the key. To my joy the thing fired off after 30 seconds of cranking! Idled rough for a few minutes but smoothed out after the air bled from the fuel lines.
The tractor ran great for about a week but on one outing the number one cylinder started blowing fuel past the injector. They shut down immediately and I towed it back to the shop and have it tore down again to the injectors. I couldn't find any installation procedure online so I figured I'd ask here.
The nut that clamps the injector in place was loose. Below is a photo of the injector plus the rocker clamp that holds it in the head. Under the right end of the clamp there's an adjustment nut on the head I suspect makes the proper degree of force to lock the injector in place. As I mentioned, every injector and clamp assembly went back in the same hole and I didn't touch the adjustment nut. When I assembled the injectors for the previous repair I tightened them with a torque wrench to the general specification for that size nut and bolt, I couldn't find any other torque values. I double checked every nut and bolt for torque on this job along the way because I didn't want to have to do the tear down again for a loose one.
I wasn't aware previously that the washers under the injectors are crush washers and are one time use. I reused them and this could be the source of the problem. I also want to be sure I'm installing the injectors properly instead of my hunch.
Does anyone know how to check the adjustment bolt on the head for the rocker clamp? If the same injector is going into the same hole and the adjustment bolt hasn't been tampered with does it need checked or adjusted? Anyone know the proper torque for the clamping nut on the rocker? I'm both frustrated and embarrassed with this job, I rarely have repairs come back like this. I'm going to redo all of the injectors while I have it apart again. Thanks in advance!
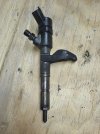
I had to disassemble a lot of engine parts to be able to pull the valve cover off and took pictures along the way. All of the injectors had to come out and I kept everything in order so all injector components went back in the same spot they came from.
Replaced the pushrods and got everything back together and held my breath when I turned the key. To my joy the thing fired off after 30 seconds of cranking! Idled rough for a few minutes but smoothed out after the air bled from the fuel lines.
The tractor ran great for about a week but on one outing the number one cylinder started blowing fuel past the injector. They shut down immediately and I towed it back to the shop and have it tore down again to the injectors. I couldn't find any installation procedure online so I figured I'd ask here.
The nut that clamps the injector in place was loose. Below is a photo of the injector plus the rocker clamp that holds it in the head. Under the right end of the clamp there's an adjustment nut on the head I suspect makes the proper degree of force to lock the injector in place. As I mentioned, every injector and clamp assembly went back in the same hole and I didn't touch the adjustment nut. When I assembled the injectors for the previous repair I tightened them with a torque wrench to the general specification for that size nut and bolt, I couldn't find any other torque values. I double checked every nut and bolt for torque on this job along the way because I didn't want to have to do the tear down again for a loose one.
I wasn't aware previously that the washers under the injectors are crush washers and are one time use. I reused them and this could be the source of the problem. I also want to be sure I'm installing the injectors properly instead of my hunch.
Does anyone know how to check the adjustment bolt on the head for the rocker clamp? If the same injector is going into the same hole and the adjustment bolt hasn't been tampered with does it need checked or adjusted? Anyone know the proper torque for the clamping nut on the rocker? I'm both frustrated and embarrassed with this job, I rarely have repairs come back like this. I'm going to redo all of the injectors while I have it apart again. Thanks in advance!
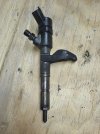