That's ok, I'll make you feel better with this. In addition toi first having done it on the wrong TDC, my idea of a wooden stick was a poor one, anyone reading it should discard the whole thing. What happens is that the stick hits the sloping side of the bowl in the top of the piston and if it slips it's unreliable. So then I tried YOUR method but with a 5mm nut instead of a 6mm allen key, put the gauge on the valve rocker and that gave me a very respectable and reliable narrow splay around the rise.
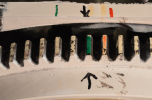
The refrence tooth is green, the first gauge move on the way up in the normal CCW direction is red, the sec ond one in reverse CW direction is green. Compression-TDC is thus at the black arrow with a VERY high degree of precision.
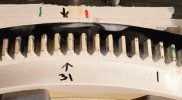
Then I marked off the end of the 10th valley (tooth) to the left and the 1/3 after the next 7th for 31 degrees (17-1/3 valleys). THAT is the drip target.
But I'm not doing the drip yet. I don't have a manual pressure pump, what kind of PSI am I looking for? I do have an injector tester I could use. If I read all the guidance correctly I should
- start at about 90 degrees before Compression-TDC
- maintain the required pressure while cranking toward it
- see a first drop forming at 31 degrees.
What am I to see after 31 degrees, a flow?