CatDieselFumes
New Member
Hello there, I figured I'd share my Moldboard pitch gauge I built for my H a couple months back. I find it very useful when running my curved edges to maintain a nice and straight edge for scraping ice and cutting shallow washboards while routine blading. Let me know what you think. If you got any questions feel free to ask. Figured this might help someone else out the way it's helped me out. Photo attached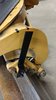
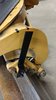