This is a great thread!
I'm not sure I'll remember everything I'd like to comment on but I'll try.
I see that you've commented that you are not particularly fond of the Terex brand. If I recall correctly CM the Screen Machine brand falls under the Terex brand of companies. I live in a place where there is a lot of on-site crushing going on and I have spent some time researching things (you've seen some of my threads) and doing some crushing myself. Some of my info is second hand but comes from what I consider to be reliable source/s. My experience is limited to track mounts and (as you know) bucket crushers.
I have direct experience crushing hard rock and concrete too. Concrete, brick, and block go through the crusher fast. You should get lots of TPH if your feed is clean. The downside is that these materials can have more of a "sandpaper" effect than many hard rock materials. This equates to faster wear on your dies (blow bars and curtains if you go with an impactor). Keeping dirt out of a jaw crusher will increase production and decrease wear. Fortunately most modern track mounts will separate fines prior to the crushing chamber. They will also give you the option to allow those fines to drop to the main belt (should you need more fines in your output) or send thme out on a separate conveyor/discharge.
I recently rented a Powerscreen PremierTrack 330. This is a smaller unit (only weighs about 75k#) so it takes less axles to move. I would think it the newest generation of LC's 300 (his spread looks to me to be Powerscreen). It only had about 60 hours on it so everything worked like new. It is NOT Duetz powered (as was mentioned as possible in a previous post) but was Cat powered and employed hydraulic drive to all components/systems. The jaw could be "burped" if jammed (run backwards for a rotation or two-never had to use this feature), and had hydraulic adjustment of the closed side of the jaw, hydraulic drive of the belt drives, feed hopper extensions and vibration/feed rate. What a joy it was to run. One of the early posters said he looked into crushing but was going to use a 30 ton excavator and a 980 loader to work with the crusher. In my experience one doesn't need that big of machines to support a crusher. Obviously the size of the crusher, how far the material needs to be shuttled, etc., matter when choosing size of support machines. In my case I loaded the crusher with my Cat 315 and used my 544j loader to handle the out put. We were feeding around 18-24" minus shot rock into the crusher to produce the 3" minus (the machine could have reduced it even farther!). My son fed the machine from an elevated platform (of the feed material) and I ran the loader to shuttle material to stock pile, clean up the pit and shuttle feed material to my son to keep enough feed withing his reach. Needless to say the loader was busy but I was able to get this done while producing about 475 tons (about 715 tons) in an eight hour day. The little trackhoe was able to keep the hopper full at the rate we were crushing. I may have been able to push the crusher harder but this was our first dance with the PT330 so we didn't push our luck and just stuck with a good steady feed rate and I had no complaints about the production rate. Setting the crusher at the proper location, and setting up your "quarry" (feed material, finished product piles, crusher locations, etc.) are important factors of production too. Part of the point here is that you can use support machines that are less expensive to own and operate (let alone transport if you provide a mobile crushing service) and still get production. Powerscreen is definitely a Terex brand but they seem to have good support across the US. I have been recently considering purchasing and looking for a MetroTrack (slightly smaller than the PT and with a few less features) and one can find them in the used market with a couple thousand hours. Probably looking at around 250-280k to buy. I was quoted $437k for the PT330 earlier this year.
I have intentionally stayed away from the SMI because of a couple reasons. First is that I'm trying to crush down to 3" minus and the unit that is in my area (JHT2650) does not do well to that size. It does well enough making 4" minus (or bigger) but it won't close enough to get to the 3" minus with consistency. The local shop that rents/sells them said that they had "special" jaw dies (as in thicker?) made to get to 3" minus but that only works until they begin to wear. There was also a major clutch issue (required a new clutch) one of my competitors had during a rental and it took several weeks to get one shipped from over seas. They had another machine come available but that still took 2 weeks. This episode happened long before the shipping/freight issues of the "post-covid" world. I know you have a good thing going with your Cat dealer but I would suggest (at a minimum) you talk to a few local customers before you drink the cool-aid on the SMI. I have had (2) fellow contractors (both with direct experience with SMI jaws) recommend staying away from this brand. I had the salesman quote me on a used JHT2650 (from their rental fleet) and I decided not to buy. On the plus side this machine was a 2015 model so no DEF, or other emissions stuff, no electronics, etc. but I needed 3" minus and had guys suggesting that I stay away.
The local Cat dealer sells Metso crushers and screens. I have had (2) people tell me that the Metso is a good brand. One guy his local the other is my brother who does custom crushing for timber companies in the PNW (he also says his Terex-Pegson MetroTrack does well but not as nice, nor as productive as the Metso -but was bought for less than 1/2 the cost of the Metso).
I've heard nothing but good things about the KPI-JCI brand (includes Pioneer). These are sold by my local Komatsu dealer so they are priced way too high (those guys are always priced high on everything!...not sure why).
BTW, I've also heard stellar reports about Komatsu track mount crushers but they are no longer sold in the US (not even sire if they make them anymore).
If you are considering anything built somewhat recently you will have to deal with emissions systems, and computers/electronics for the control systems (which don't seem to like dust and/or vibration) and lots (LOTS!) of panic buttons all over the machine.
If I wanted to further reduce overhead I would consider a 60' stacker (can be moved with a pick-up) to reduce, or even possibly eliminate the need for the loader to stockpile out put material.
If you are only going to crush concrete I would suggest looking at the Rebel crusher as well. When I looked into them I felt as though they were knowledgeable and they flat told me that their product, though it would do the job, was not the best option for hard rock crushing. I liked that as most salesman simply tell you whatever they think will sell the product. On the plus side the Rebel is only about 40K#, comes with screens (will also return oversize to the crusher), can be had as an impactor or a jaw (not many jaws out there with screens attached), and will cost about 200k less than "main stream" track mounts. I can not speak to their ability to provide support and/or service. I would think that you may have more success with service since you are much closer to where they are made than I am.
If you go with any of the crushers you've mentioned thus far (as a jaw) you will likely have to screen to get the products you have stated that you want to make. This is an area that I have only dipped my toe into and can have a greater impact on cost and production than the crusher can (the crusher will likely crush as fast as you can load it-depending upon how small you will crush to of course).
As it relates to rebar, I usually hammer to remove the bar. A processor might be faster but you already own the hammer. Plus it makes you feed size smaller which can increase production. I charge money to dump at my place and, while rebar is okay, I don't take any woven wire because its a tire killer for anything less than loader tires. If I had a magnet I would have no problem with the wire. I've seen guys park a trailer under the magnet belt so that they don't have to handle the metal twice. Just let the trailer fill and then go dump it at the recycler.
Below are some pictures showing delivery day of the PT330.
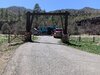
Computer control systems
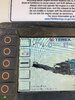
At this location we handled the out put with a skid steer (we didn't go very far with it and didn't have but maybe a thousand yards to crush here).
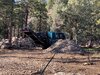