Legdoc,
It's a Servo II CNC bed mill like the picture below. It has a not so common ISO 40 taper spindle. All the tool holders are secured with a power drawbar. The spindle is a bit larger than a Bridgeport style mill and the holders are a lot more rigid than R-8 tooling. They were popular in the '90s and I don't think they are made anymore, but you can get parts for it. What I love about the machine is it's a hybrid. You can use it as a manual mill with a DRO or CNC program in 3 axis. Very handy since a lot of my repair work does not need CNC capabilities for simple one-off parts.
I'm very blessed to have access to my friend's commercial machine shop. It is well equipped with 2 of these mills, 6 Haas CNC vertical mills, and a CNC live tooling lathe, surface grinders, a waterjet cutter, and a wire-cut EDM. Plus all the basic manual lathe, mill, drill press, band saws, etc. There is also an unbelievable amount of tooling to equip a job shop. In addition, there is a complete weld shop with MIG, TIG, stick, and oxy-acetylene.
Are you into machining?
Steve
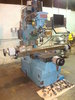