Thank you for all the advice. Let me give a little bit more context...This a remote location in the Sahara desert. We have been operating in that area for the past year and half. We setup a quarry, a crusher and an asphalt plant in that area without mains power or easy water access. We have been doing a mill and overlay project of an airport runway. This new effort is for the construction of a new runway hence all the earthworks equipment and paving equipment.
I am not coming at this totally blind. We have dealt with 120F heat, rainstorms with winds upwards of 60mph, sandstorms, floods...
My estimates on parts availability are not guesses, but what we have experienced. We have had to procure parts from Europe, the US and China to deal with mechanical failures and have a pretty good logistics train to make that happen. My concern is not the logistics....We know how to handle that. I am trying to hear about people's experiences in remote locations and the things/tools/methods they have used to maintain this type of equipment. Like I said, parts supply is something we know how to resolve. I just want to make sure that I give the guys the tools they need to do the job.
Additional context, we have dirty diesel that will in many cases be contaminated (we know this becuase we have had to deal with multiple fuel pump, injector failures). We are looking at potentially installing a diesel polishing/cleaning machines.
I came to this forum to get multiple viewpoints specifically because this is a complex issue and hearing different viewpoints you can start to pull out some common threads and form a reasonable appreciation of the issues involved.
Please review the first message on this tread for the list of equipment that will be onsite. We have very capable mechanics and guys used to working in a touch environment. What they have not had is access to the best tools. We are now in a position to provide that.
This is how I am envisioning this:
1-Preventive Maintenance
2-Corrective Maintenance
3-Parts and consummables
4-Tools and equipment
5-Staffing
6-Supplies Management
1-Preventive Maintenance:
We will be procuring all maintenance kits for all the machines anticipating a total of 3000 hours of operation on all machine. Most machines will have between 4000-6500 hours on them. Based on that all parts will be stocked on site to do the scheduled maintenance
2-Corrective maintenance:
This in my mind is obviously where the most challenging aspect of this effort is. Murphy being on the staff, we can expect surprises. Having said that, all we can do is plan for habitual failures based on our field experience (Fuel quality, what we had to fix on our machines before) and that of others on these machines (you guys...). What I need to figure out here after talking to the dealer is what are the parts most likely to fail during 3000 hours or work assuming that we have done a proper inspection of the machines before shipping them Iincluding SOS analysis). If we have a failure for which we do not have the part available, then like I said we can procure it and transport to site, 5-10 days we can handle and is within acceptable bounds.
Catastrophic failures of machines is also something we can cover to some extent. We will have machine redundancy for some of the equipment that we are not able to mobilize regionally.
3-Parts and consummables: This is I think is the easy part, it is just a matter of identifying all the kits, gather all the greases, lubricants, oils and shipping...Not going to lose sleep over this
4-Tools and equipment: I need some advice here, beyond the essentials what type of tools can make the difference in being able to restore a machine fast. For example, we will have the necessary devices to read and analyze machine codes.
- Compressors
- Pneumatic Tools
- Tire repair kits
- Grease/lubing gear
- First aid kits and safety gear
- Jacks
- Welding equipment
- Hand tools
- Bench tools(vises, etc...)
- Engine lifts
-
etc...This is the easy stuff...I am sure my guys will give me a longer list, but beyond the obvious stuff are there other tools that one should have onsite?
5-Staffing: Having the right folks for the job. We have 3 of our own mechanics, we will have a mechanic from the local CAT dealer (1000km away) and 2-3 guys from South Africa.
6-Supplies Management: Obviously making sure that we are always stocked and anticipate parts and consumable needs. One thing that I need to take a guess on is how many replacement tires do we need to be on the safe side (Assuming again that we have good tires to begin with).
This is long enough. I just watned to provided context.
Thank you for all the input.
Realized the original list did not include equipment specs:
* 6 graders (CAT 120M, 4 of them with GPS)
* 8 wheel loaders (CAT 966, CAT 924)
* 5 dozers (CAT D4,D6,D9)
* 6 Rock dumps (CAT 740)
* 4 Case IH tractors with pull scrappers(STX 480)
* 10 compactors (2 soil, 6 asphalt, 2 pneumatic) -CAT or HAMM...
* Several Passenger trucks (Toyota Land Cruisers, we know how to deal with these)
* 2 pavers (Vogele 1800-2, we have a 1600-2 already and know how to maintain and fix it really well, we just had to replace the auger chain and rebuild the whole screed).
See pictures of our current installation. We already have a camp setup,we have 3 office containers with AC and plan on installing 2 additional ones for the repair crew as work/storage areas.
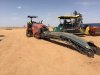