ThreeCW
Well-Known Member
When we bought our 2006 CAT 242B skid steer (SN - BXM03117) 3 years ago, there was some catch up maintenance and repairs required that I have been addressing the past few years.
After repairing a pilot valve leak (detailed in another thread), we still had an oil leak that needed fixing. It turned out that the mounting bolts on the Left Hydraulic Drive Motor had loosened slightly, resulting in a leak of lub oil from the Left Drive Chain Case, past the sealant around the Left Hydraulic Drive Motor, into the belly pan and on to the floor under the 242B.
I was able to reduce the leak by tightening up the 10 Drive Motor mounting bolts, but over time, the lub oil leak has increased again, and more prescriptive repair measures are required. It is still just a nuisance leak with perhaps 1 to 2 tablespoons of lub oil ending up under the machine after each use, but I am getting tired of putting a drip pan under it … and even more tired of the leak when I forget to pull out the drip pan and run it over!
My plans include removing the Left Drive Motor, replace the Drive Motor mounting bolts (10 pieces), washers and lock nuts and then reinstall the Drive Motor with new flange sealant. That’s the Reader’s Digest version.
Does anyone have experience with pulling and reinstalling a drive motor on this type of skid steer?
Are there any suggestions, do’s or don’ts that I should be aware of?
Can anyone provide a repair procedure that I can review before proceeding?
Thank you and Regards, 3CW
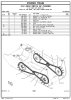
After repairing a pilot valve leak (detailed in another thread), we still had an oil leak that needed fixing. It turned out that the mounting bolts on the Left Hydraulic Drive Motor had loosened slightly, resulting in a leak of lub oil from the Left Drive Chain Case, past the sealant around the Left Hydraulic Drive Motor, into the belly pan and on to the floor under the 242B.
I was able to reduce the leak by tightening up the 10 Drive Motor mounting bolts, but over time, the lub oil leak has increased again, and more prescriptive repair measures are required. It is still just a nuisance leak with perhaps 1 to 2 tablespoons of lub oil ending up under the machine after each use, but I am getting tired of putting a drip pan under it … and even more tired of the leak when I forget to pull out the drip pan and run it over!
My plans include removing the Left Drive Motor, replace the Drive Motor mounting bolts (10 pieces), washers and lock nuts and then reinstall the Drive Motor with new flange sealant. That’s the Reader’s Digest version.
Does anyone have experience with pulling and reinstalling a drive motor on this type of skid steer?
Are there any suggestions, do’s or don’ts that I should be aware of?
Can anyone provide a repair procedure that I can review before proceeding?
Thank you and Regards, 3CW

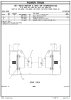
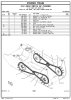