treemuncher
Senior Member
I've had to pull another one of my hard to access & thread through hydraulic lines again. It got me to thinkin' about how the other mechanics pull some of these difficult to thread hoses through a machine. I did not see any threads for these "tricks of the trade" so I thought maybe I should share what works for me in the event that maybe it will help someone else. Hopefully, others will chime in with even better ideas or what they like to use/do on difficult hose replacements.
While working on my Lamtrac with a leaking main seal of the travel motor puking hydraulic fluid into the final planetary drive, I did some troubleshooting on the case drain line that had been recently starting to leak. This is one of the worst lines to replace on the machine as it is one of the longest and goes through numerous transitions through the track frame, into the main frame, bends 180 under the pumps then back through the right main frame and up into a return manifold located on the hydraulic tank. I replaced that line with a new one less than a year ago when I had the track frames off of the machine....in order to avoid what I had to go through today. At least the motor was already out so I had a little extra wiggle room and it was not as packed with dirt as it normally is.
After capping the drained hose, I tested it with air pressure and a soap mix. The fitting was leaking where the factory crimped the collar onto the 90 degree fitting. I could move it a good 5 degrees of rotation. There was enough extra hose to allow my local shop to chop the bad fitting off and crimp on a new one. I did not look forward to the R&R of this hose.
After removing the straight end from the manifold block, I taped a 3/8 rope to the end of the hose to follow the routing path of the hose and provide a pull rope to reinstall. Normally, I prefer to use MuleTape or Dyneema cord but I was too lazy to find what I needed. MuleTape is much slicker and stronger than any most rope out there. Dyneema is just about the same but round and expensive.
Of course with a choice of pulling the 90 fitting or the straight, it is a no brainer to pull out the straight fitting as the tag end and reinstall the straight fitting first. Just tying or taping a rope on that straight fitting was not going to make for any easy pull(and likely would have come off) or push so I made up a quick fitting on the lathe out of aluminum. I tapped the base with 1/2" NPT so that I would likely be able to use this with other hoses via adapters to NPT. I had a #8 ORFS male X #8 NPT male for this particular hose so I was good to go. The hose armor also made R&R much easier after I slicked it up with some of my soap mix used for air testing the leak.
For this particular tool, I used some 3/8" MuleTape that should be rated for at least 1200 lbs pull. The knot is recessed and held in by the adapter fitting. I will break a lot of other stuff before I can break this loop on a pull. A strong unit like this is needed when using ratchet straps to pull a hose through a machine.
With the cone adapter, the installation went fairly smooth. I had to get the assembly through some other hose guarding that wrapped with 2 other hoses. Just a taped on rope was NOT going to cut it for this job. This is not my first pulling cone that I've built. I keep one in my service truck for the next pilot hose that I have to install on my PC200 - THAT was the hose that made me come up with this particular idea for a pulling tool several years ago. I hope this can help someone else on their next "mission impossible".
While working on my Lamtrac with a leaking main seal of the travel motor puking hydraulic fluid into the final planetary drive, I did some troubleshooting on the case drain line that had been recently starting to leak. This is one of the worst lines to replace on the machine as it is one of the longest and goes through numerous transitions through the track frame, into the main frame, bends 180 under the pumps then back through the right main frame and up into a return manifold located on the hydraulic tank. I replaced that line with a new one less than a year ago when I had the track frames off of the machine....in order to avoid what I had to go through today. At least the motor was already out so I had a little extra wiggle room and it was not as packed with dirt as it normally is.
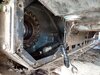
After capping the drained hose, I tested it with air pressure and a soap mix. The fitting was leaking where the factory crimped the collar onto the 90 degree fitting. I could move it a good 5 degrees of rotation. There was enough extra hose to allow my local shop to chop the bad fitting off and crimp on a new one. I did not look forward to the R&R of this hose.

After removing the straight end from the manifold block, I taped a 3/8 rope to the end of the hose to follow the routing path of the hose and provide a pull rope to reinstall. Normally, I prefer to use MuleTape or Dyneema cord but I was too lazy to find what I needed. MuleTape is much slicker and stronger than any most rope out there. Dyneema is just about the same but round and expensive.
Of course with a choice of pulling the 90 fitting or the straight, it is a no brainer to pull out the straight fitting as the tag end and reinstall the straight fitting first. Just tying or taping a rope on that straight fitting was not going to make for any easy pull(and likely would have come off) or push so I made up a quick fitting on the lathe out of aluminum. I tapped the base with 1/2" NPT so that I would likely be able to use this with other hoses via adapters to NPT. I had a #8 ORFS male X #8 NPT male for this particular hose so I was good to go. The hose armor also made R&R much easier after I slicked it up with some of my soap mix used for air testing the leak.

For this particular tool, I used some 3/8" MuleTape that should be rated for at least 1200 lbs pull. The knot is recessed and held in by the adapter fitting. I will break a lot of other stuff before I can break this loop on a pull. A strong unit like this is needed when using ratchet straps to pull a hose through a machine.
With the cone adapter, the installation went fairly smooth. I had to get the assembly through some other hose guarding that wrapped with 2 other hoses. Just a taped on rope was NOT going to cut it for this job. This is not my first pulling cone that I've built. I keep one in my service truck for the next pilot hose that I have to install on my PC200 - THAT was the hose that made me come up with this particular idea for a pulling tool several years ago. I hope this can help someone else on their next "mission impossible".